Examples
Example 1. Ethyl Benzene Process: Recycle Column
In the Ethyl Benzene (EB) process there is a stage to separate Benzene (B) from the product stream using a distillation column. The flow of distillate (D stream) and bottom product (B stream) are manipulated variables to control the condenser and the sump levels. The pressure of the column is controlled by manipulating the heat duty of the condenser. The temperature of the 14th stage (starting from the top) affects the product quality. This variable is controlled by manipulating the reboiler heat duty.
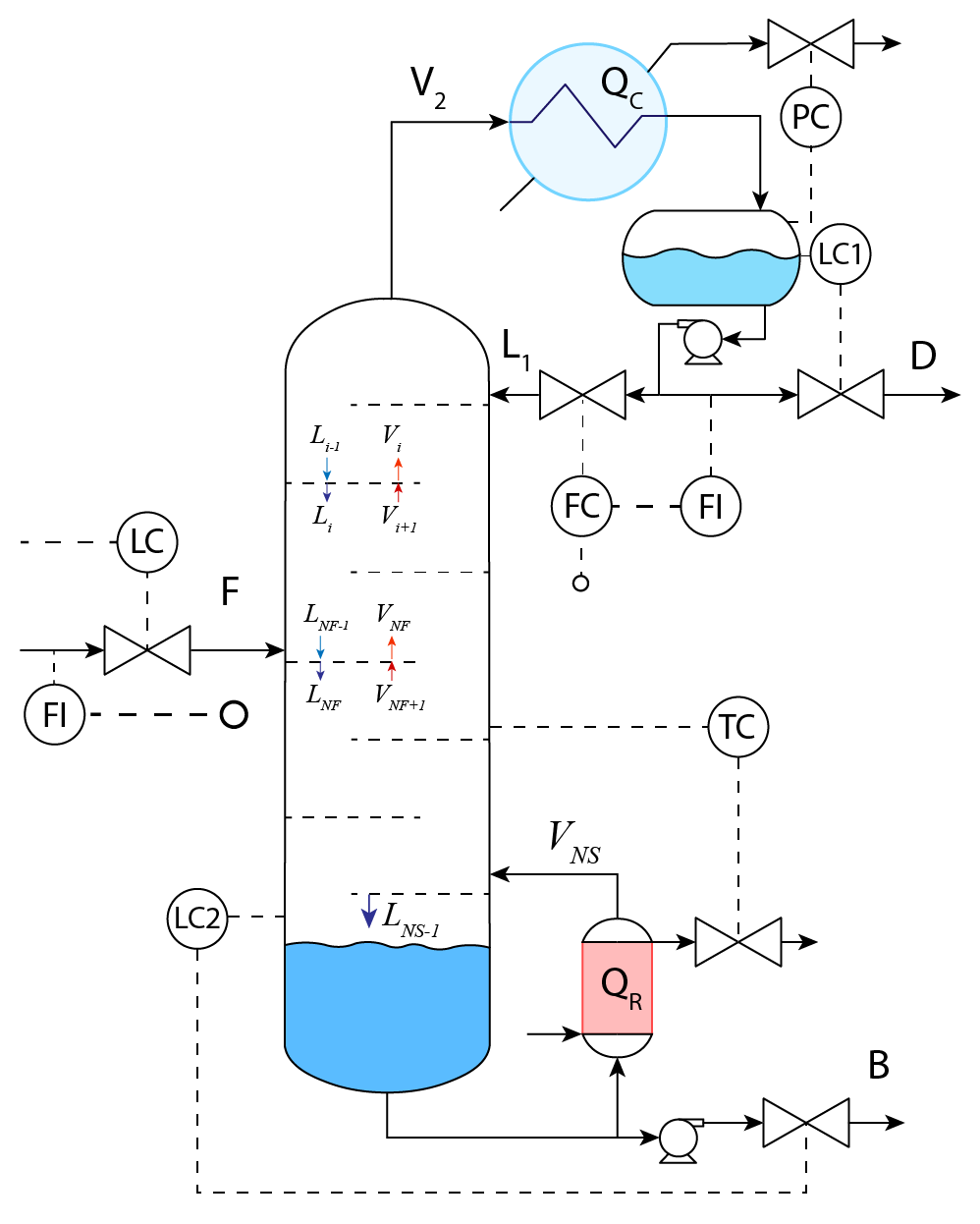
The process information is shown in Table 1.
Table 1. Process informations |
Property |
Description |
Unit |
Stream F |
Stream D |
Stream B |
---|---|---|---|---|---|
Mole fraction |
E |
% |
0.0001 |
0.0001 |
- |
B |
% |
0.5146 |
0.9989 |
0.0003 |
|
EB |
% |
0.3354 |
0.0010 |
0.6905 |
|
DEB |
% |
0.1500 |
- |
0.3092 |
|
Temperature |
K |
432 |
314 |
390 |
|
Pressure |
atm |
0.39 |
0.3 |
0.5 |
|
Volume flow |
m3/hr |
250 |
88.5 |
135.5 |
Insights:
The distillate and the bottom product are highly inversely correlated with the reflux drum level and the sump level signals.
The condenser and reboiler duties have a strong positive correlation with the stage 1 pressure and stage 20 temperature signals.
The level has a ramp response while the temperature and pressure have first-order responses.
We assume reflux drum level, sump level, Stage 1 pressure and last stage temperature as Controlled variables (CV) and the distillate flow, bottom product flow, condenser duty and reboiler duty as manipulated variables (MV). In the following sections, the distillation column is identified using different available models in SysID Add-on.
ARX Model
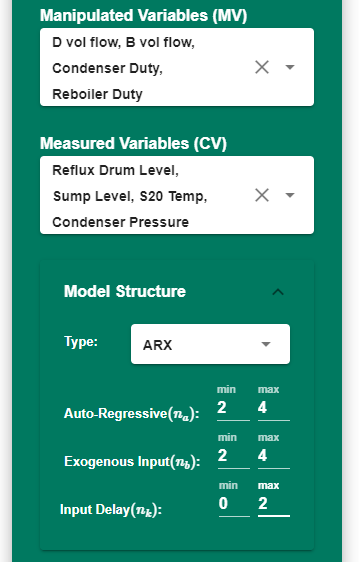
Select MVs and CVs from the left panel.
Manipulated variables:
Distillate flow
Bottom product flow
Condenser duty
Reboiler duty
Controlled variables:
Reflux drum level
Sump level
Stage 1 pressure
Stage 20 temperature
Select minimum and maximum range for the model order and the input delay.
Select training and validation conditions.
Click on ‘Identify’ to start the identification process. The hyperparameter optimizer obtains the best model order and delays to minimize the prediction error.
Click on “Push Model” to push the Seeq Formula to the Seeq Workbench.
To avoid overfitting and capturing the noise of the signals, select lower maximum order for the ARX model.
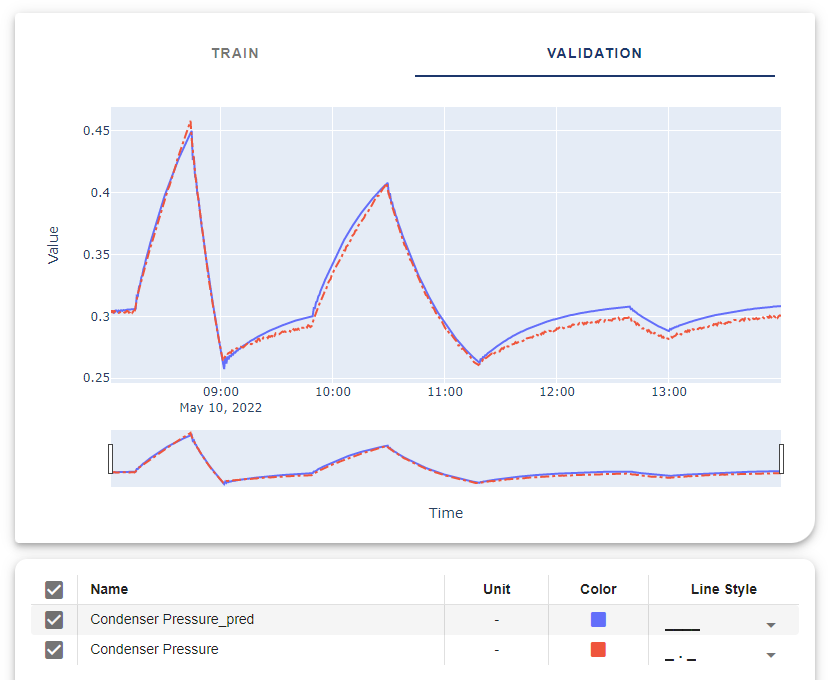
Sub Space Model
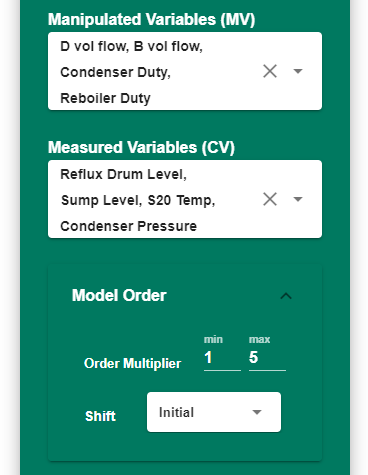
Select MVs and CVs from the left panel.
Manipulated variables:
Distillate flow
Bottom product flow
Condenser duty
Reboiler duty
Controlled variables:
Reflux drum level
Sump level
Stage 1 pressure
Stage 20 temperature
Select minimum and maximum range for the order multiplier. A lower multiplier leads to lower-order models.
Select shift method.
Select training and validation conditions.
Click on ‘Identify’ to start the identification process.
Click on “Push Model” to push the predicted data to the Seeq Workbench.
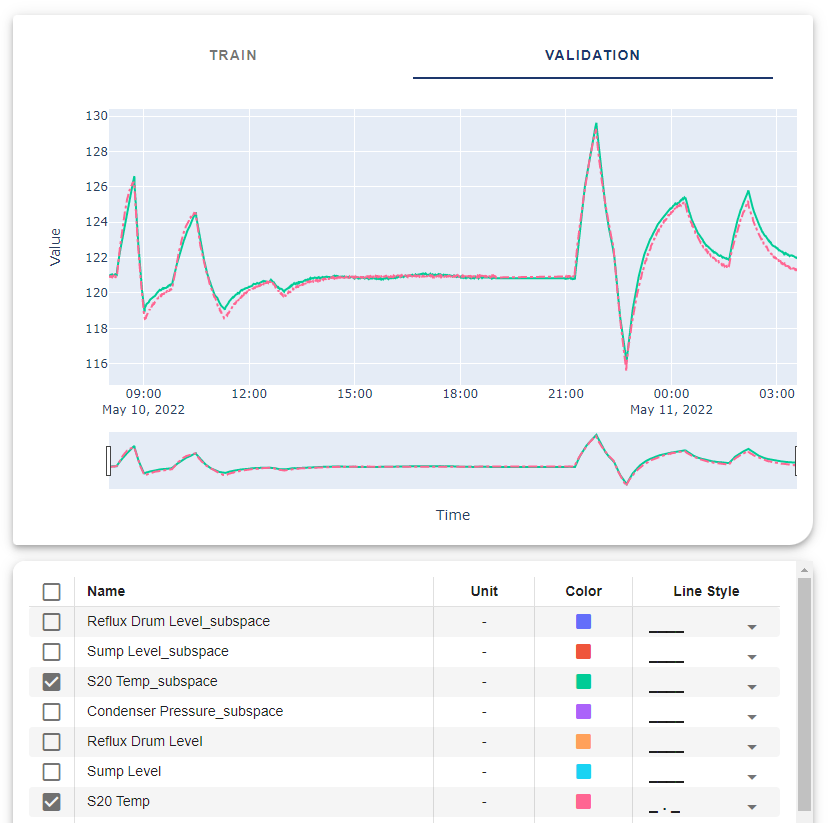
Neural Network Model
Select MVs and CVs from the left panel.
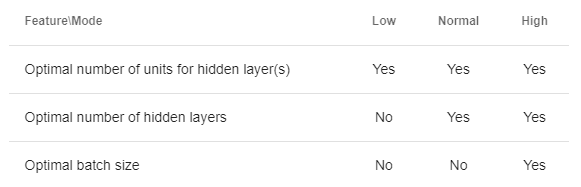
Manipulated variables:
Distillate flow
Bottom product flow
Condenser duty
Reboiler duty
Controlled variables:
Reflux drum level
Sump level
Stage 1 pressure
Stage 20 temperature
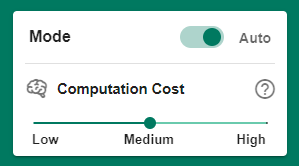
Select the computation mode.
Select training and validation conditions.
Click on ‘Identify’ to start the identification process.
Click on “Push Model” to push the predicted data to the Seeq Workbench.
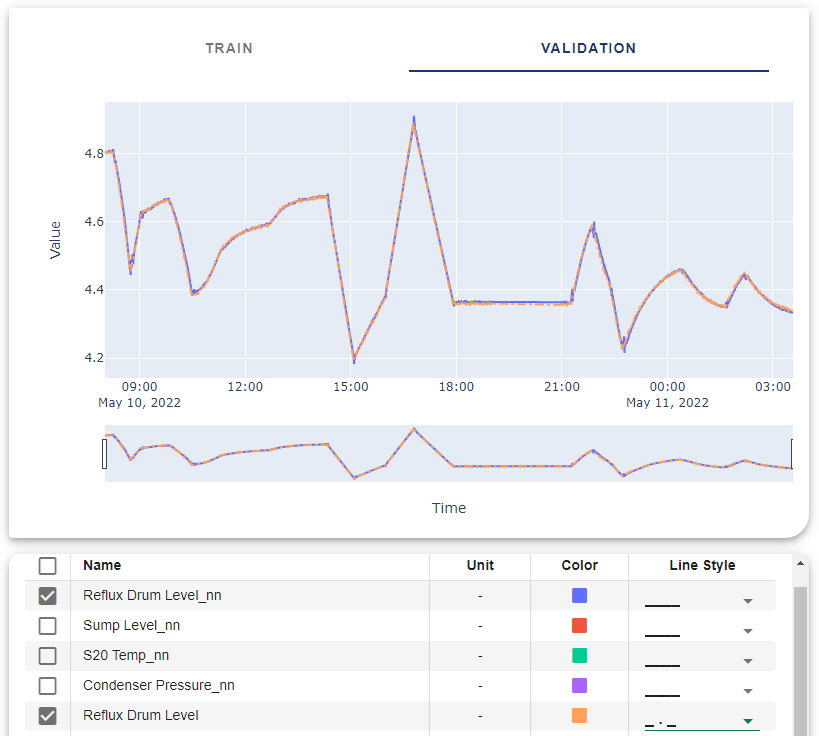
Transfer Function Model
This model requieres more knowledge about the system identification and data selection. Otherwise it will end up with no solution for the problem or the identification process takes more time to run.
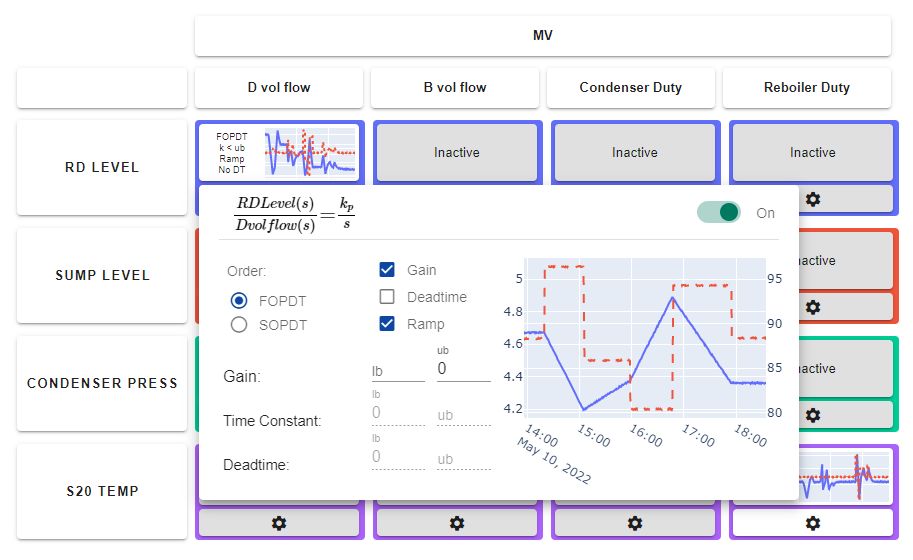
Select MVs and CVs in the setup page.
Manipulated variables:
Distillate flow
Bottom product flow
Condenser duty
Reboiler duty
Controlled variables:
Reflux drum level
Sump level
Stage 1 pressure
Stage 20 temperature
Select training and validation condition. (Optional) This setting can be set and override in the Matrix page by clicking on the CV buttons. Click on ‘Next’ button.
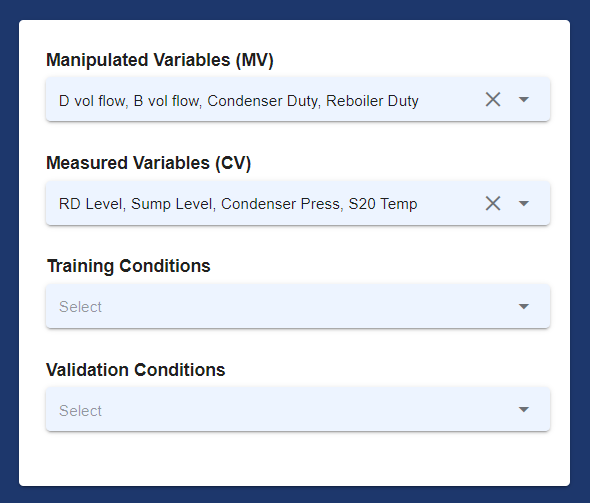
Modify the identification matrix. Inactive unnecessary terms by right-clicking on them or switching them off in the setting menu.
Select the model structure based on the system behavior.
Enter lower bounds and upper bounds for each available term in the equation. (Optional)
Modify and override training and validation conditions by clicking on the CV labels.
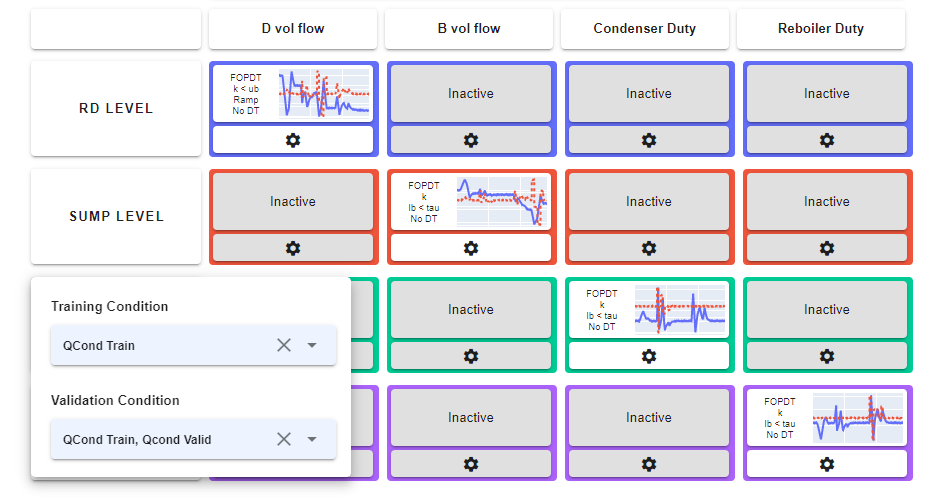
Click on ‘Next’ button to start the identificaiton process. Step response will be shown up after this process.
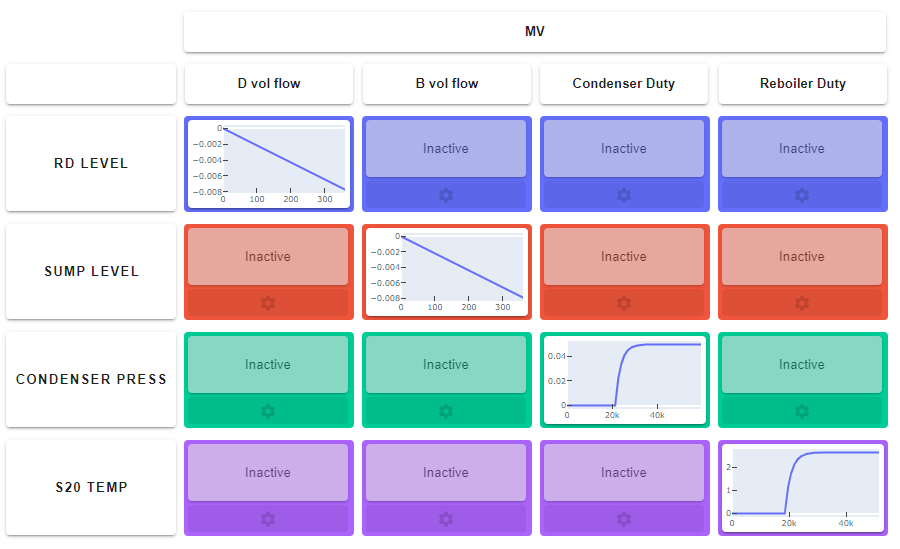
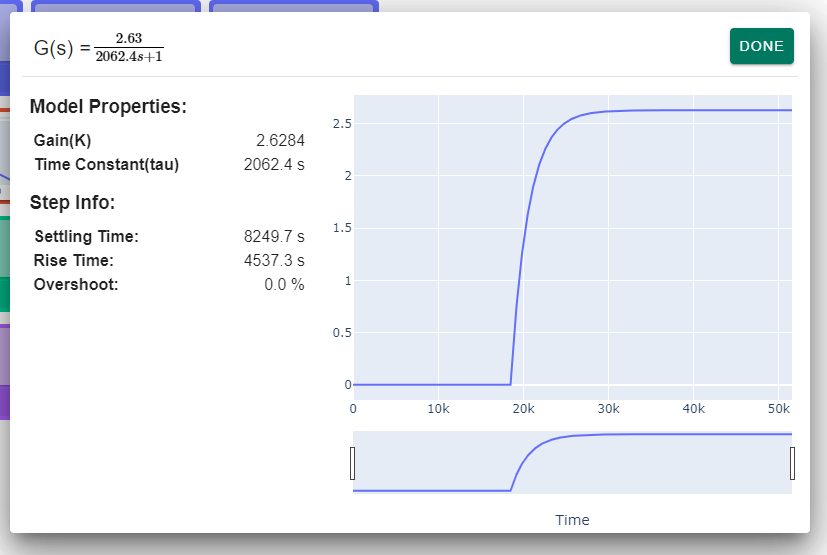
To plot training and validation results click on ‘Next’ button.
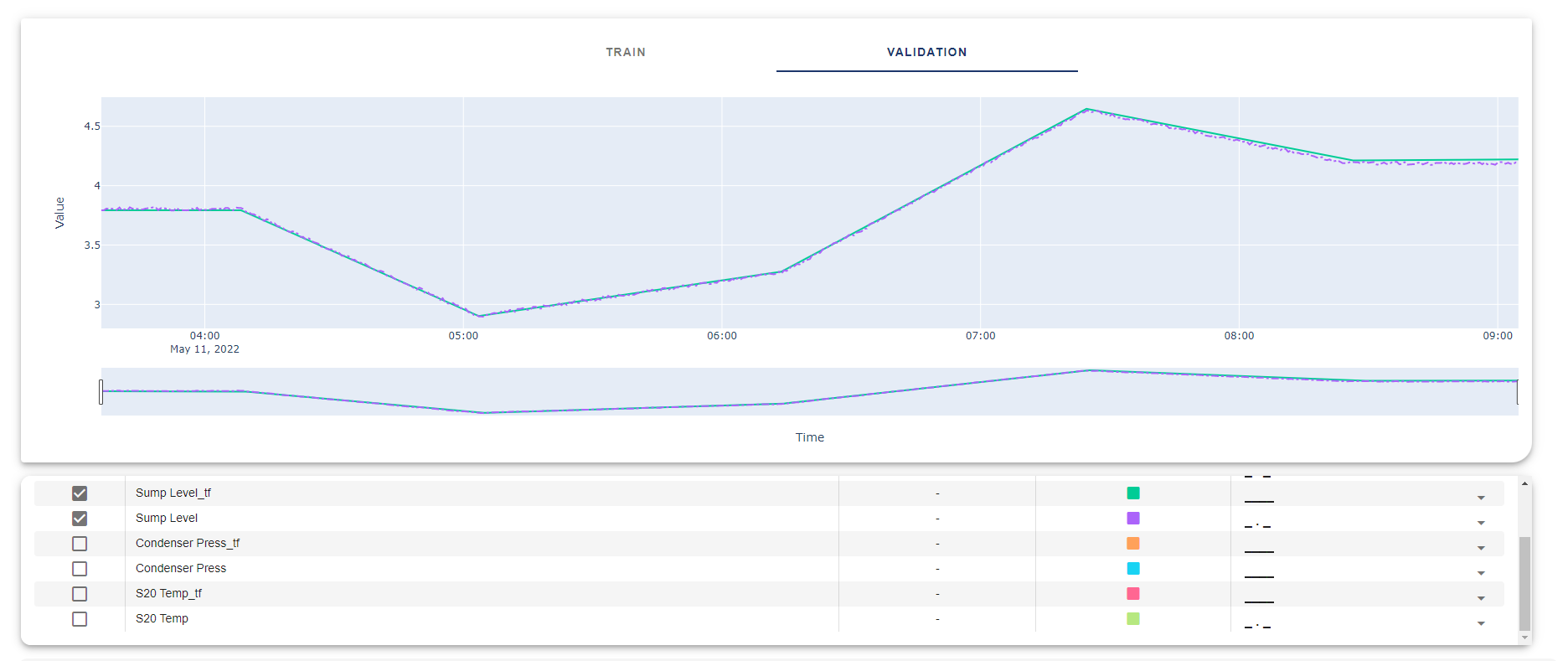
Click on “Push Model” to push the predicted data to the Seeq Workbench.
Example 2. Two Series Reactors
In this example an exothermic reaction occurs in two series reactors. Component A is the limiting reagent. The reaction conversion rate is calculated based on the concentration of component A . The temperatures of both reactors
are controlled by manipulating the cooling water flow rate.
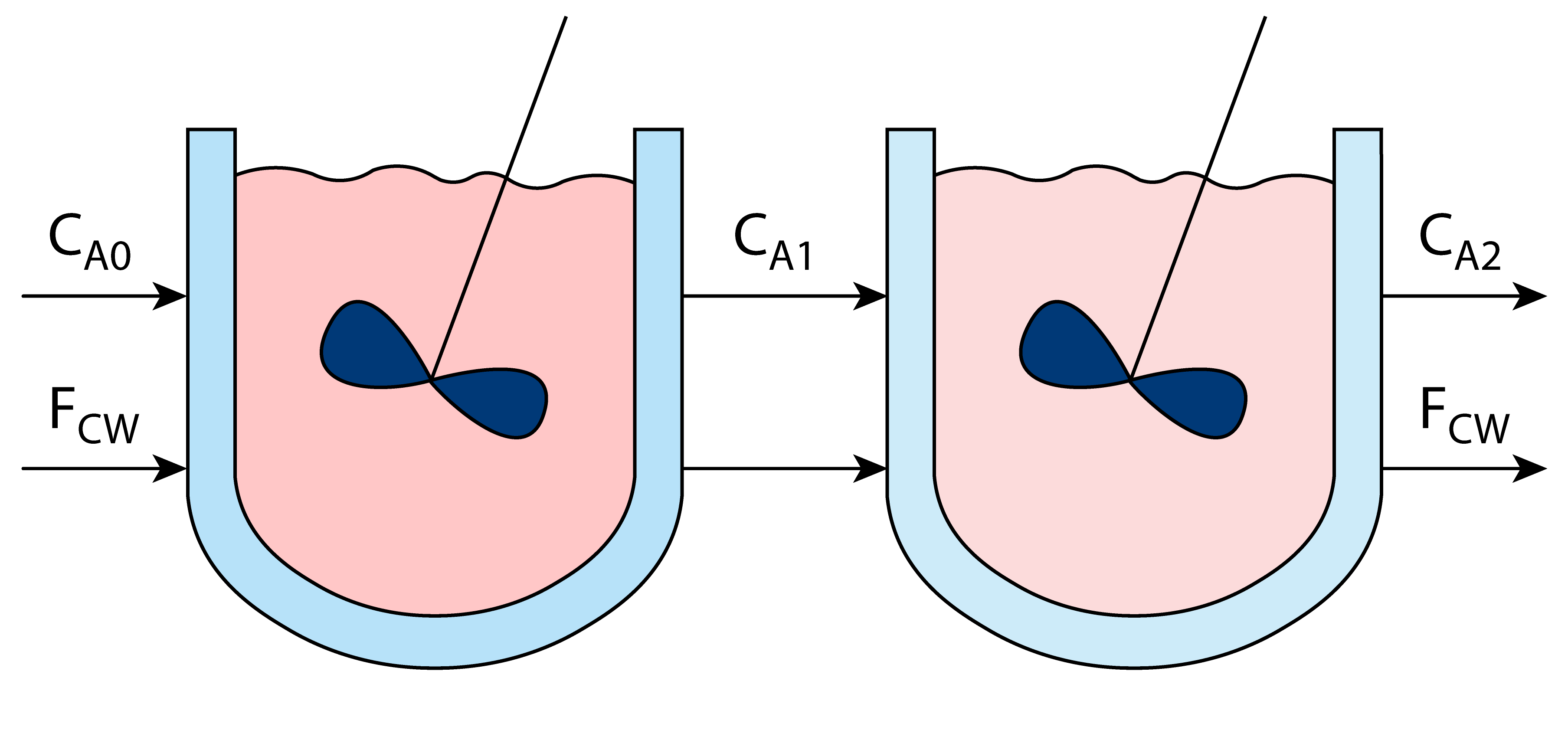
Insights:
The reactor’s temperatures are highly inversely correlated with the cooling water flow rate signal.
The concentrations of component A have a strong positive correlation with the cooling water flow rate signal.
ARX Model
Select MVs and CVs from the left panel.
Manipulated variables:
Cooling water flow rate
Controlled variables:
The reactor 1 Temperature
The reactor 2 Temperature
The concentration of component A in the reactor 1
The concentration of component A in the reactor 2
Select minimum and maximum range for the model order and the input delay.
Select training and validation conditions.
Click on ‘Identify’ to start the identification process. The hyperparameter optimizer obtains the best model order and delays to minimize the prediction error.
Click on “Push Model” to push the Seeq Formula to the Seeq Workbench.
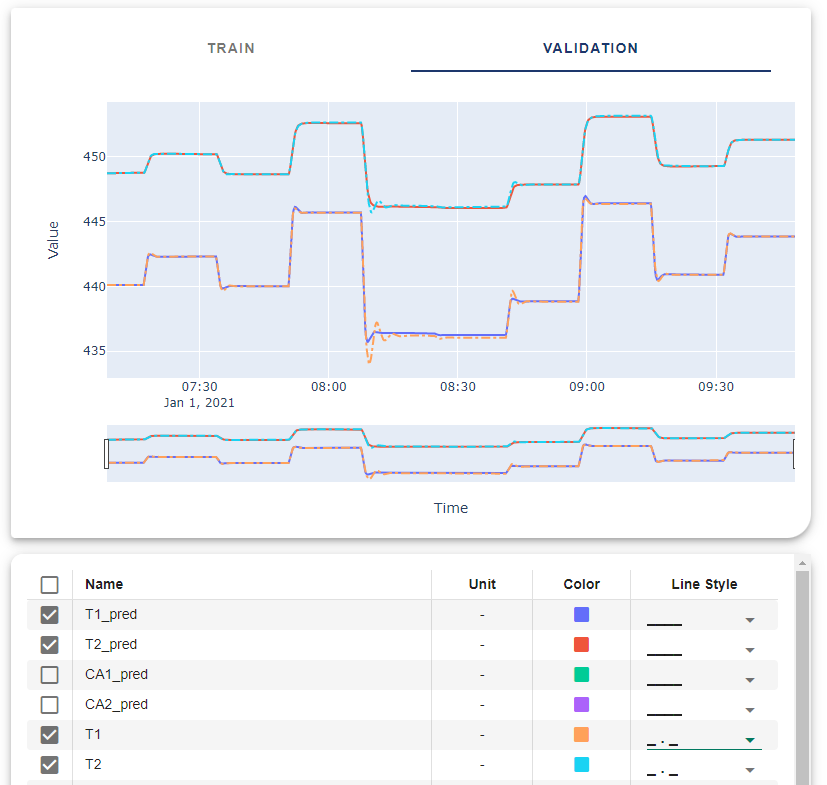
Sub Space Model
Select MVs and CVs from the left panel.
Manipulated variables:
Cooling water flow rate
Controlled variables:
The reactor 1 Temperature
The reactor 2 Temperature
The concentration of component A in the reactor 1
The concentration of component A in the reactor 2
Select minimum and maximum range for the order multiplier. A lower multiplier leads to lower-order models.
Select shift method.
Select training and validation conditions.
Click on ‘Identify’ to start the identification process.
Click on “Push Model” to push the predicted data to the Seeq Workbench.
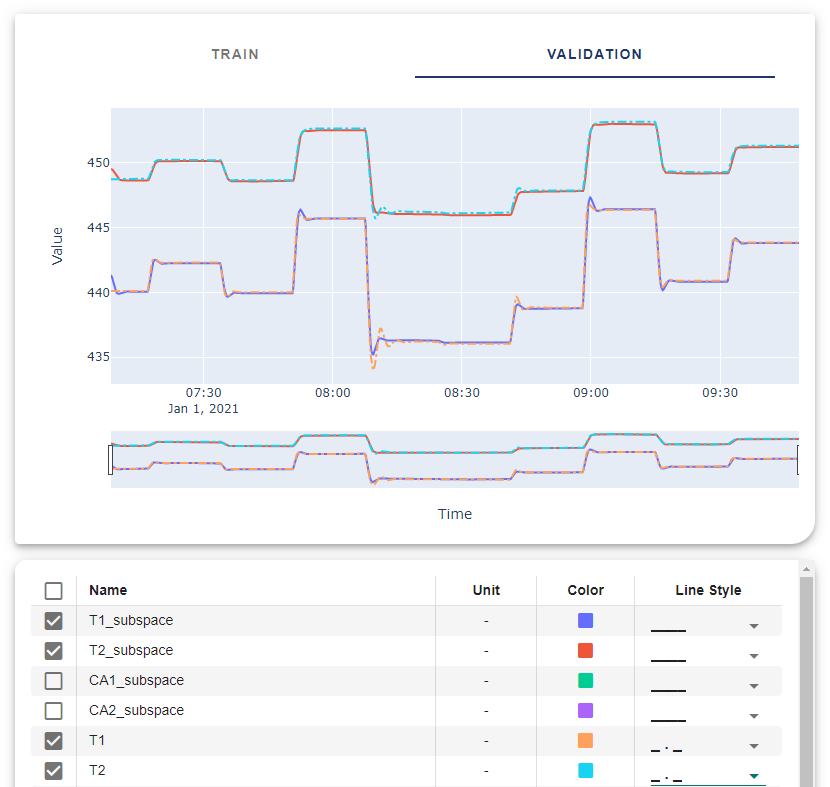
Neural Network Model
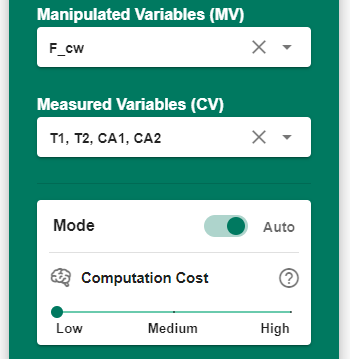
Select MVs and CVs from the left panel.
Manipulated variables:
Cooling water flow rate
Controlled variables:
The reactor 1 Temperature
The reactor 2 Temperature
The concentration of component A in the reactor 1
The concentration of component A in the reactor 2
Select the computation mode.
Select training and validation conditions.
Click on ‘Identify’ to start the identification process.
Click on “Push Model” to push the predicted data to the Seeq Workbench.
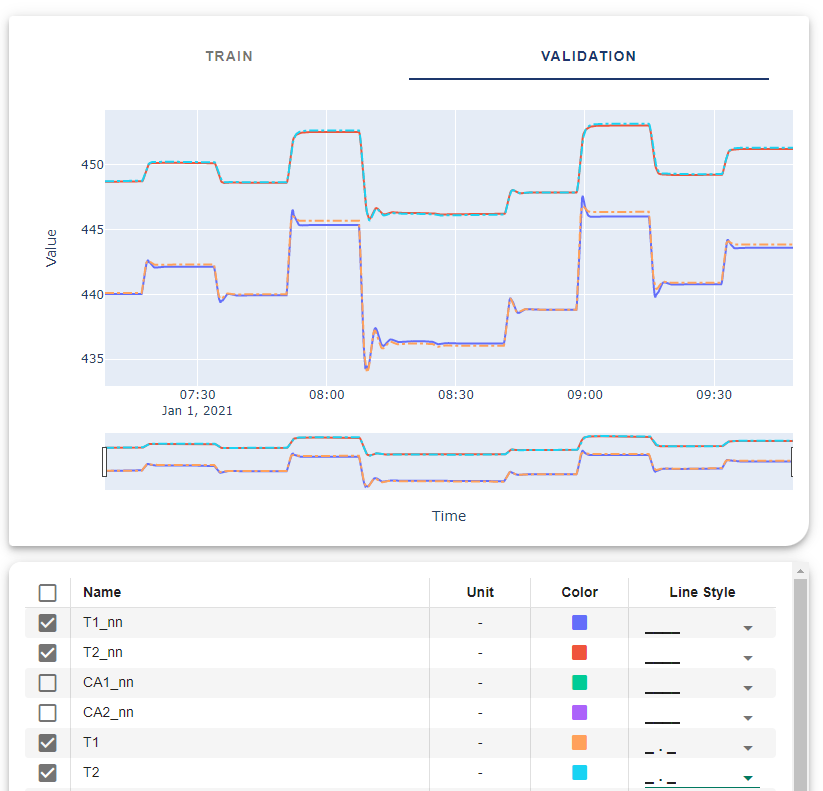
Transfer Function Model
This model requires more knowledge about system identification and data selection. Otherwise, it will end up with no solution for the problem or the identification process takes more time to run.
Select MVs and CVs on the setup page.
Manipulated variables:
Cooling water flow rate
Controlled variables:
The reactor 1 Temperature
The reactor 2 Temperature
The concentration of component A in the reactor 1
The concentration of component A in the reactor 2
Select training and validation condition. (Optional) This setting can be set and override in the Matrix page by clicking on the CV buttons. Click on ‘Next’ button.
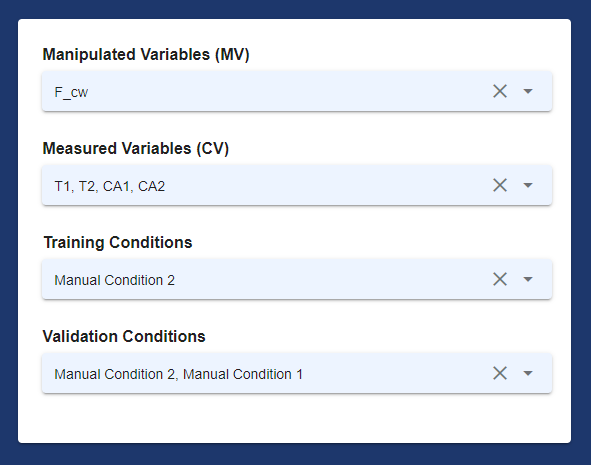
Modify the identification matrix. Inactive unnecessary terms by right-clicking on them or switching them off in the setting menu.
Select the model structure based on the system behavior.
Enter lower bounds and upper bounds for each available term in the equation. (Optional)
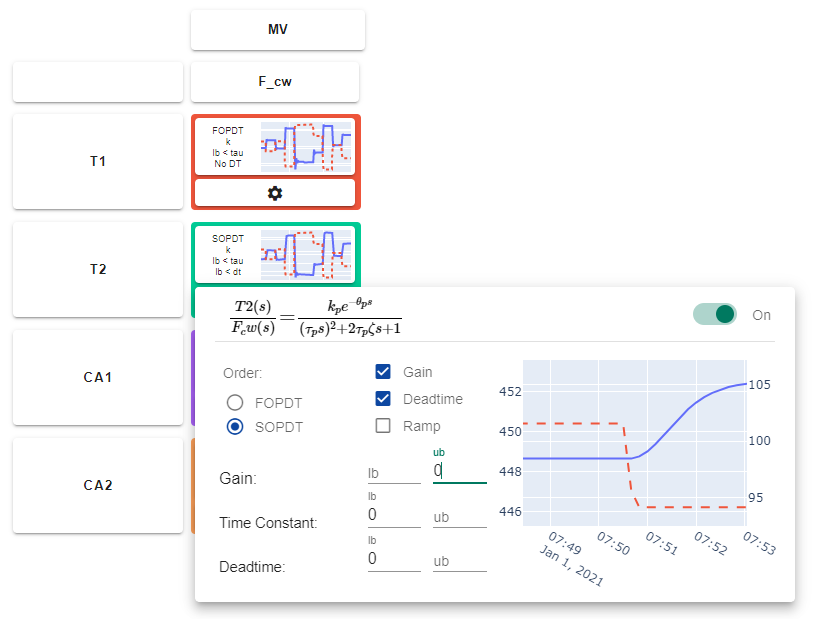
Click on ‘Next’ button to start the identificaiton process. Step response will be shown up after this process.
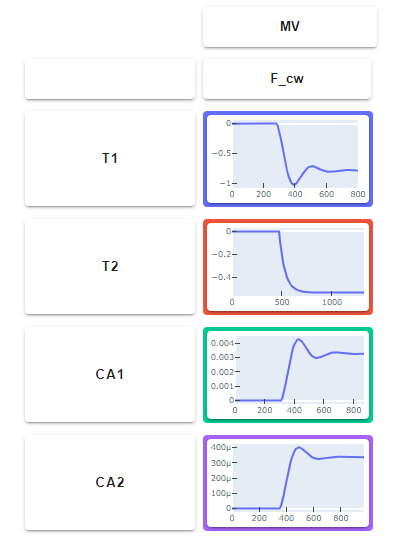
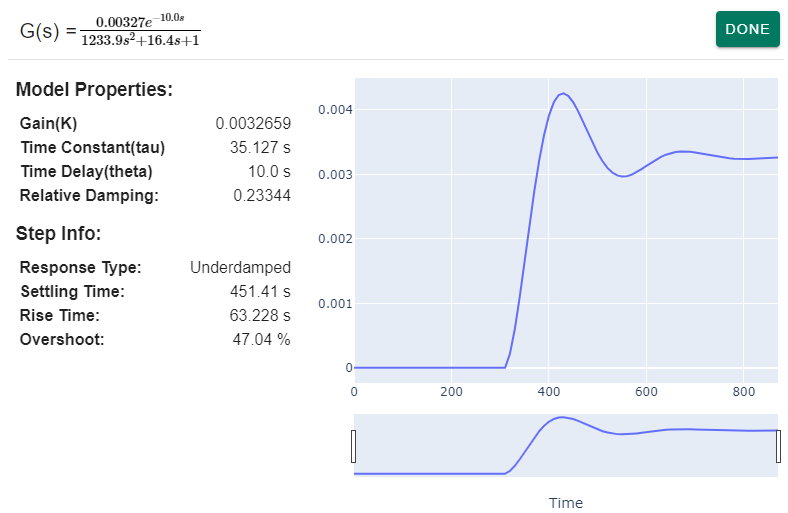
To plot training and validation results click on ‘Next’ button.
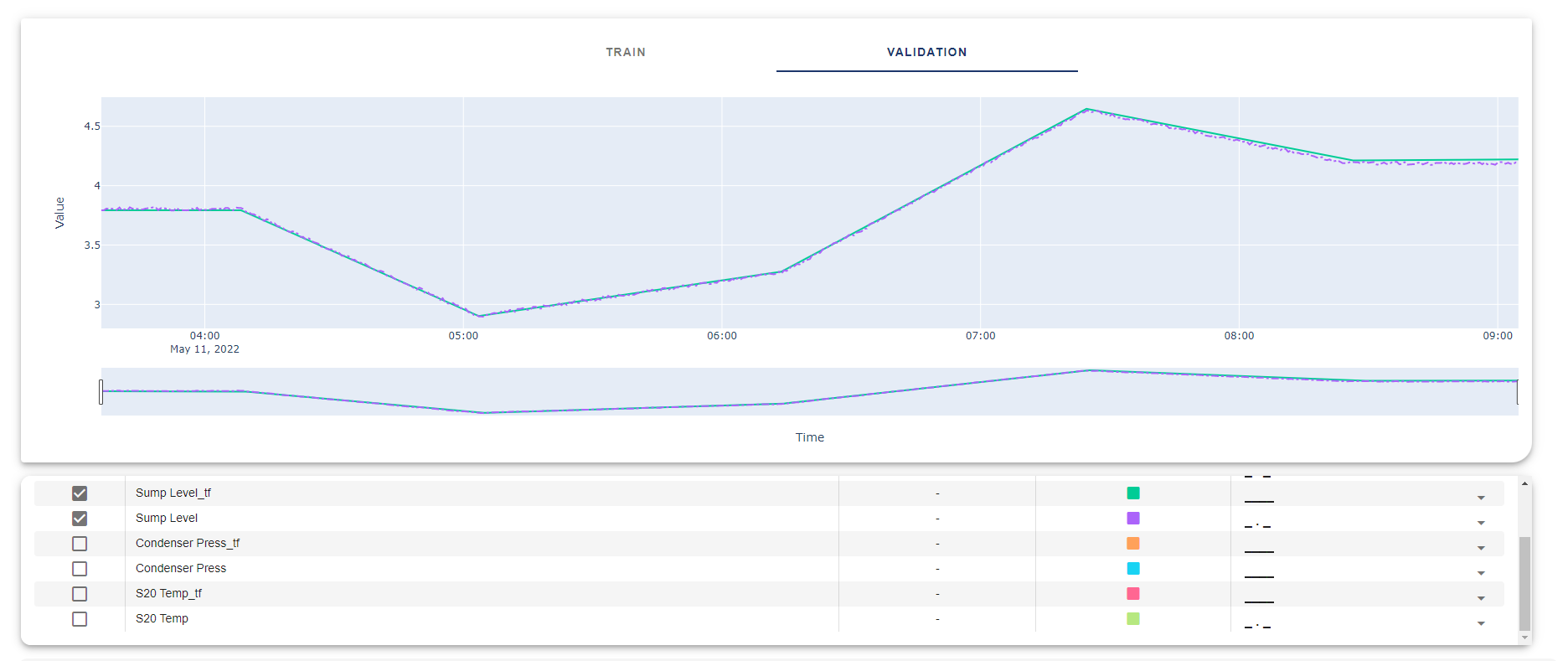
Click on “Push Model” to push the predicted data to the Seeq Workbench.